Seeking a more optimized conservation method, CEO of FDC Enterprises Fred Circle initiated a collaboration with Orkel, reducing energy crop loss while securing better working conditions for his employees.
FDC Enterprises
FDC Enterprises is an American company present doing business across 26 US states east of the Rockies. Established in 1995, it is conservation and bioenergy that represent the very core of FDCE’s professional expertise.
Consisting of a highly proficient team, they maintain their status as market leaders through the combination of a hands-on work ethic and research-driven partners. Naturally, for the forward-leaning business, it was a question of time before they started looking into efforts to reduce annual energy crop loss from their 4,400 acres of energy crops.
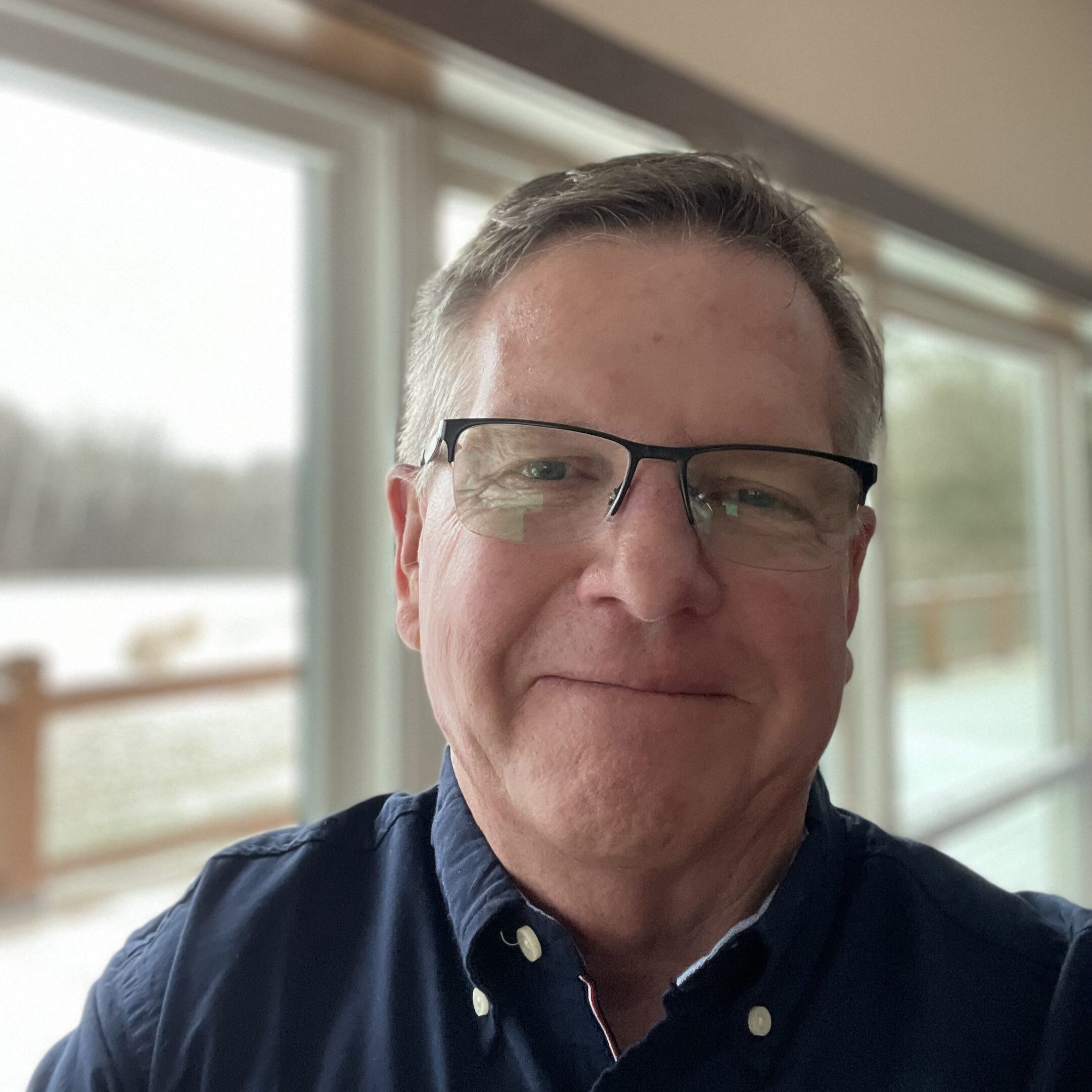
15% Material Loss
“We were losing an average of 15% revenue generation every year in crop loss due to spoiled material from molding”, says Mr. Fred Circle, President & CEO of FDC Enterprises. “Additionally, we were on the lookout for further cost saving efforts such as removing the need of tarping.” Essentially, the company was seeking improved ways to utilize their resources, consisting mainly of miscanthus and switchgrass.
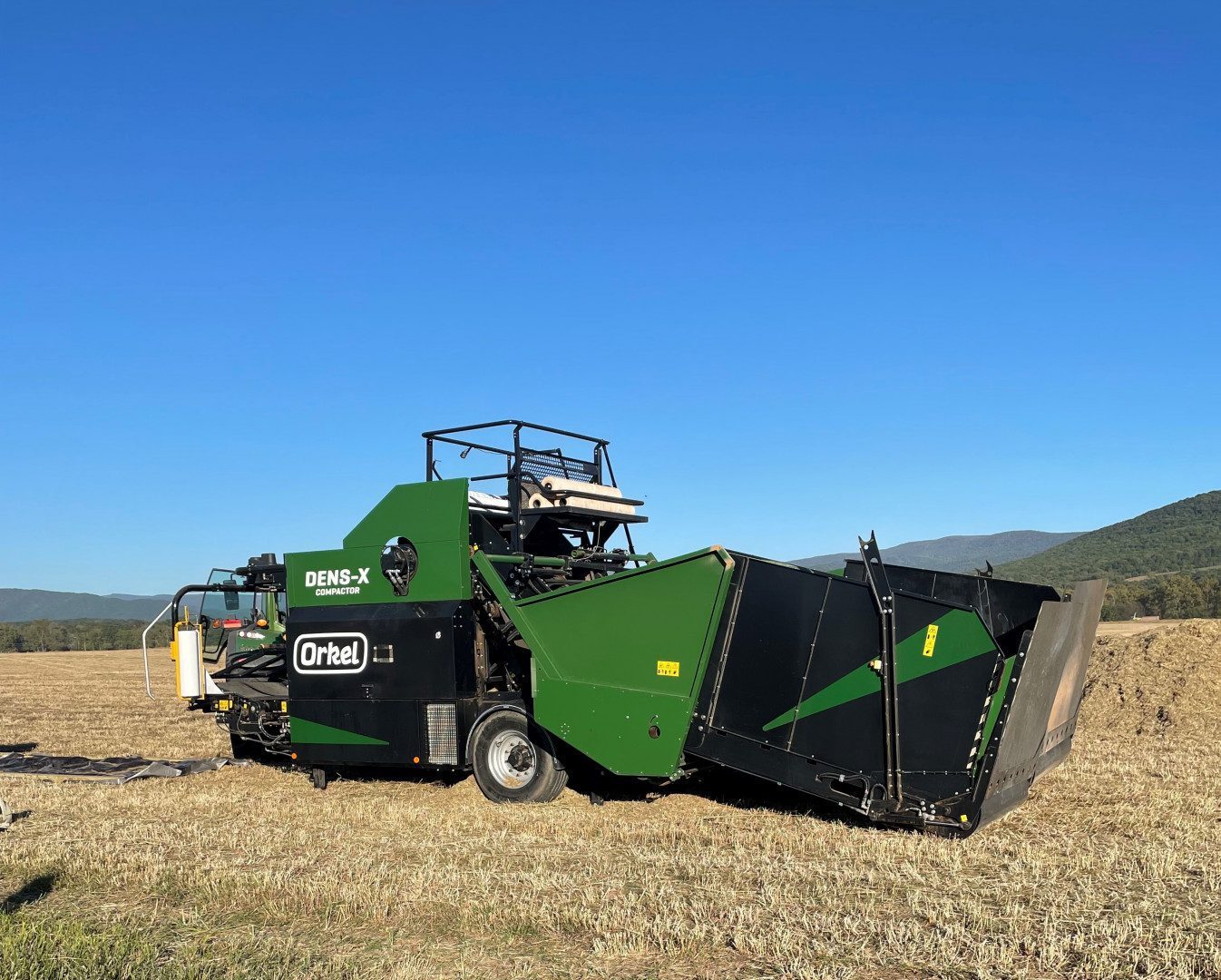
Investment Payback
After FDCE’s collaboration with Orkel’s Georgia-based technician Will Bennett, it is apparent that American-based machine expertise played an important part in FDCE’s final decision: “One of the reasons to why we chose Orkel was their ability to provide close support of the machine, both in terms of technical expertise and for optimization purposes.” Mr. Circle continues: “Up-time is important to us, because everything we do is season-dependent.”
12,000 Tons of Crops Demanding High-Density
The primary reason for investment, however, was the Orkel high-density technology. Due to the demand for high-capacity and high-density machinery, the Orkel Dens-X compactor was an ideal fit. Processing about 12,000 tons of crops each year, FDC Enterprises was seeking a solution which reduced the amount of moldy material, an unfortunate result from oxygen supply during crop storage.
Increased baling density improves overall conservation, resulting in a high value product. Based on previous experience of bale density, Orkel ‘s Dens-X compactor helped FDCE’s annual quality control loss percentage to drop from 15% to 1-2%, offering significant environmental and financial gains for the company.
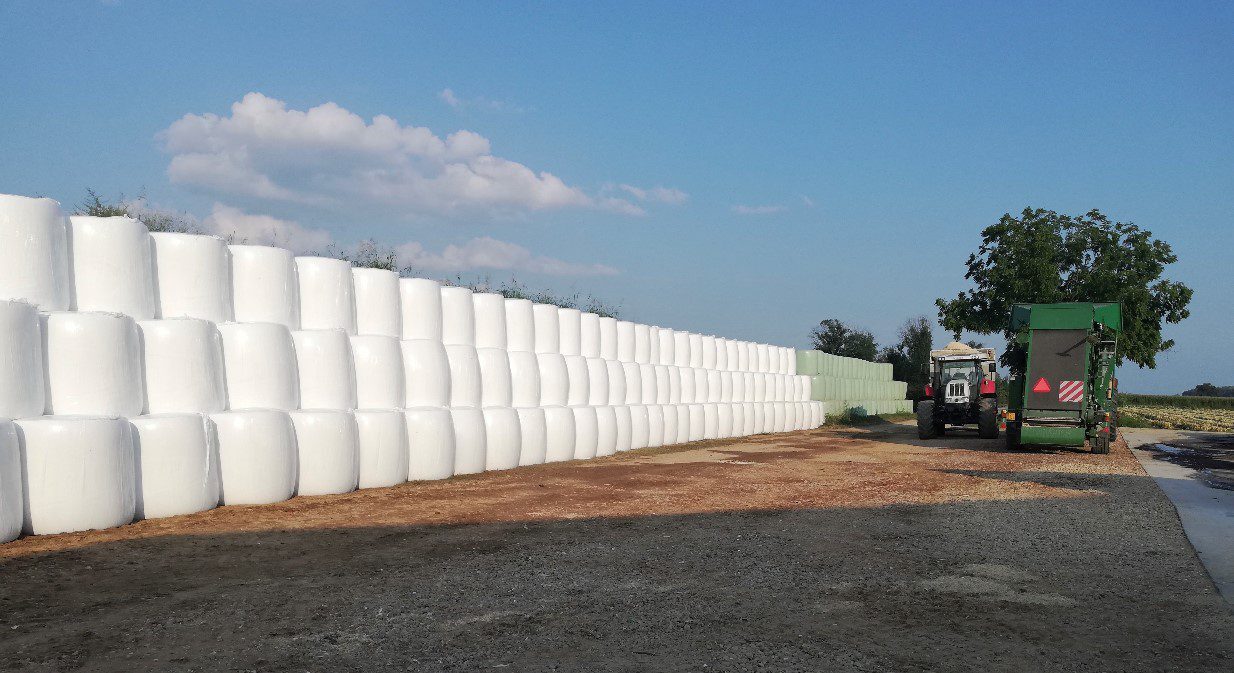
Logistical Advantages
After introducing high-density bales into their production line, FDCE also experienced logistical benefits in addition to reduced crop loss. Baling with an Orkel Dens-X compactor, they have cut storage and labor costs associated with stacking and tarping square bales. Logistically, the crop bales are easier to move while also providing a more consistent and stable production.
Removing Hazard from Working Conditions
Profitability is one aspect of the equation, just as the human aspect is another. Circle explains the concern for his employees, who used to grind up the previous square bales to access the crops, releasing mold into the work environment. “Despite wearing protection such as pressurized masks, I don’t want my guys working under those conditions.” Nor were they able to identify sufficient efforts to solve the issue: “We can’t remove it [the mold] once it’s there, as there is no way of separating it from the material itself once it’s baled.”
By improving their conservation method, they’re finally able to redirect their focus to other optimizable parts of their production. “The compactor technology opens new Dens-X revenue generation opportunities that can potentially get rid of waste streams within the local community while also sustaining and creating jobs” exclaims Circle. “In the end, it’s about what we do and what we bring to our local communities.”

A Story to Tell
Throughout the month of January, FDCE baled more than 5,500 high-density bales, equal to 2,700 tons of material. This is visible though the Orkel telematics system on their machine, which provides insight into the bale production as well as the bale contents. Asking about FDC Enterprises’ future, Mr. Circle expects a demand for increased capacity in the upcoming years.
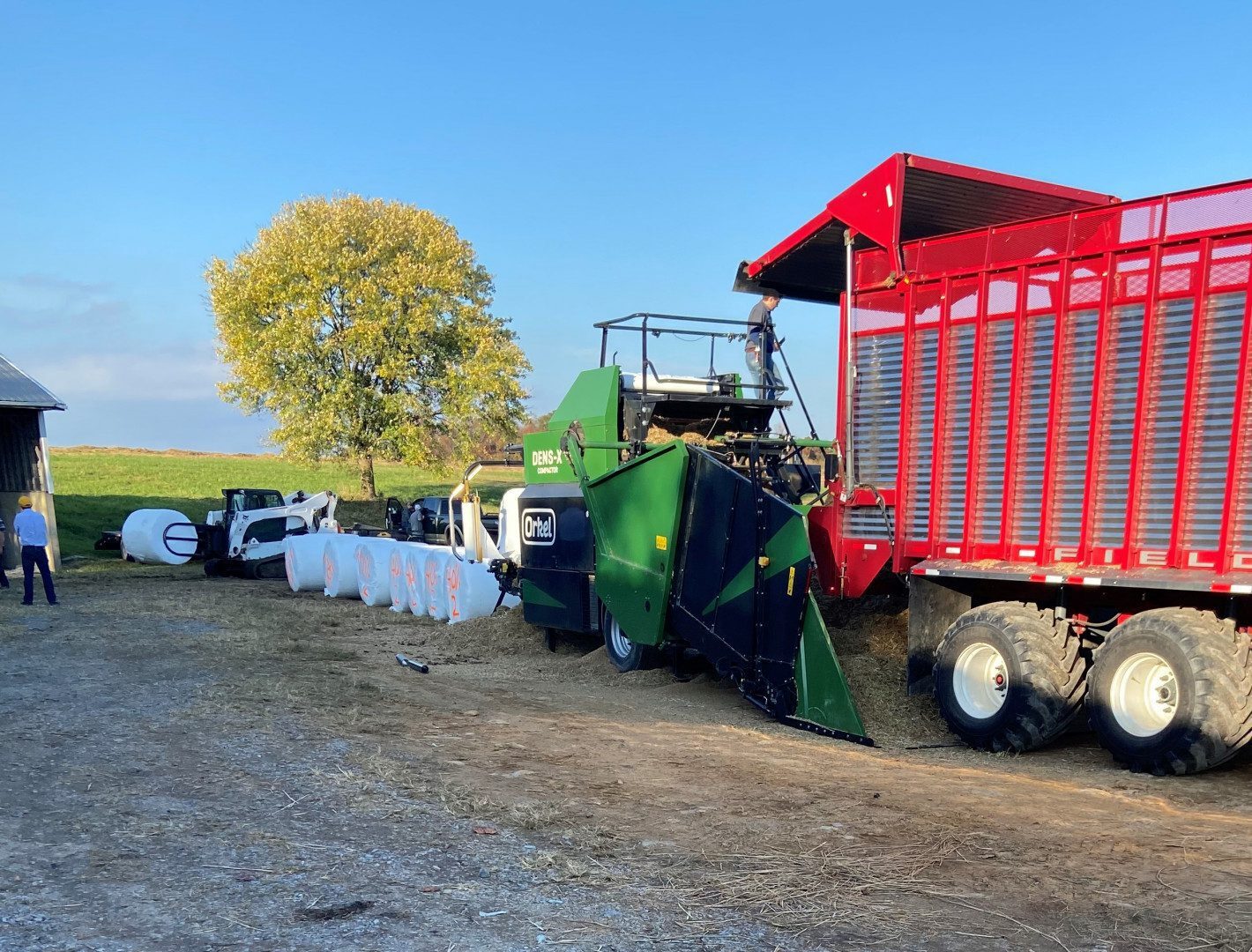
“I would recommend Orkel technology as we’re extremely happy with the machine.” He adds: “[The technology] Broadens the opportunities in our core business, in addition to making us more efficient and environmentally responsible. On the cutting edge of technology, the Orkel [compactor] provides another story to tell.”