Bale your sugar beet pulp, it carries three significant advantages compared to traditional storage in bunker silos/bags! Firsty, pulp ensiled in bales will cool down faster, retaining the high quality material. Secondly, the pulp may be fed as early as two weeks after baling. And thirdly, if properly handled, the pulp should suffer no nutritional losses.
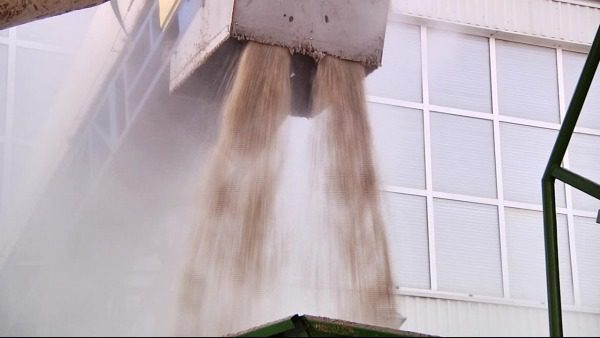
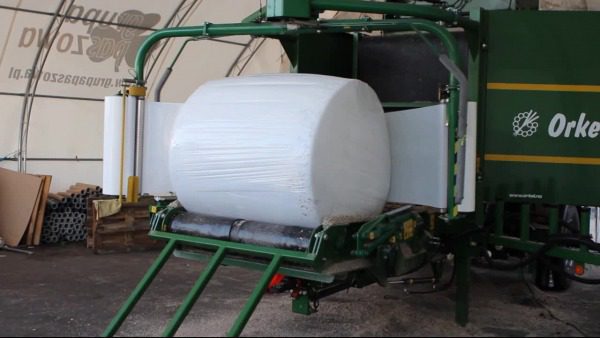
Film wrapping excludes oxygen from the beet pulp
Expect faster cooldown when you bale sugar beet pulp
Beet pulp in bales is an excellent fodder. The pulp is at its best if the pulp is ensiled hot (>50 degrees celsius) and with high density. When ensiled in a bale, the pulp cools down much faster than in bunker silos or bags. You can feed these bales after two weeks of storage, compared to a bunker or bag silo where you must wait a minimum of 6 weeks.
Farmers confirm that the pulp ensiled in bales is of the highest quality, even after a year of storage! Moreover, baling sugar beet pulp is very convenient for the farmer. After opening and feeding a bale, the remaining bales stay closed, retaining 100% of their quality. Optimal handling prevents the pulp from suffering nutritional losses.
Content of 1 kg DM | Unit | Maize silage 27% DM | Beet pulp in bales |
Raw fibre | g | 212 | 208 |
General protein | g | 88 | 111 |
Raw fat | g | 33 | 11 |
Nitrogen-free compounds | g | 615 | 599 |
Sugar | g | 31 | |
Calcium | g | 10,9 | |
Phosphorus | MJ | 0,9 | |
Energy NEL (net Energy of lactation) | 6,3 | 7,4 | |
Deutche Landwirdschafts-Gesellschaft 1997 |
Nutritional value of sugar beet pulp in bales compared to maize silage
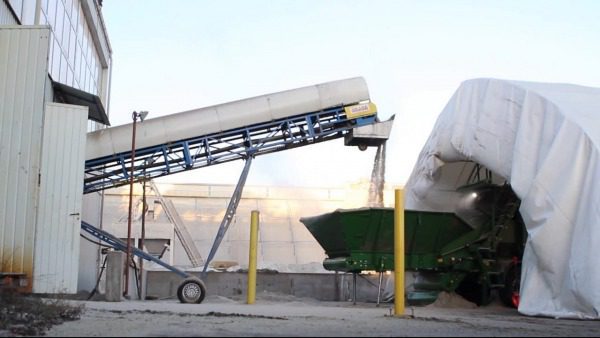
Beet pulp directly from the conveyor into the feed hopper
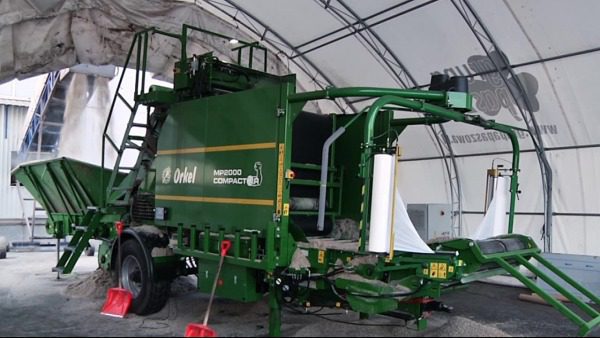
The beet pulp is compacted inside the chamber of the Orkel compactor
Easy and efficient operations
The bale production process takes place at the sugar factory near the pulp tray. The material is transported from the feed hopper of the compactor into the chamber, where a compact bale is formed. Widefilm or net is applied in the chamber, before the bale is finally wrapped in stretch film. The average bale weight is 1.2 tons. For loading bales of pulp, loaders with special grippers adapted for this purpose are used. Bales can easily be stored and handled with a bale grabber.
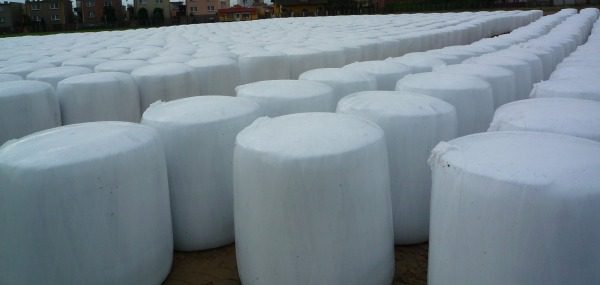
Sugar beet pulp stored in Orkel bales
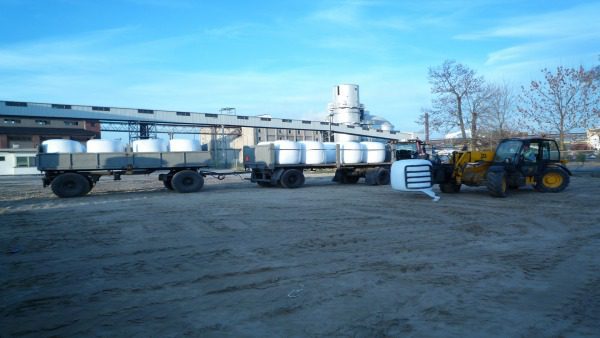
Beet pulp in bales provide easy logistics
Main benefits with baling sugar beet pulp
- Avoidance of aerobic processes that are progressing if pulp is stored and transported in open air
- Faster “cooling down” that means silage is ready as a forage earlier.
- Very convenient usage. Opening and distribution of a bale do not harm remaining silage by exposing it to an air unlike in silo or in a bag.
- Possibility of long storage without losses of nutrition properties / values
- Retaining high properties all around the year unlike silage in silo or in a bag that during Summer time is very fast losing nutritional value.
More than 600.000 beet pulp bales since 2007
In 2006, sugar factories in Poland carried out successful baling tests of beet pulp using the Orkel MP2000 compactor. The coming year, the first Orkel compactor started baling frequently, making a total of 30.000 sugar pulp bales. The following years, more Orkel compactors were requested to meet the growing demand. Since then, over 600.000 bales of sugar pulp has been made with Orkel compactors, and the demand is continuously increasing.
Overall, one may conclude that the best pulp silage is made from ‘hot’ raw material directly from the conveyor at the sugar factory; And the most profitable way to conserve the material is by baling it with an Orkel compactor!
We would love to tell you more about sugar beet pulp baling.
Contact us today at sales@orkel.no / +47 948 14 010